A key USP of the Valgro Edge Breaker Series is its ability to deburr fine blanking parts and plastic-coated sheets while preserving the surface quality and protective plastic layer.
This ensures that the deburring process focuses solely on edge burrs, without causing any damage to the surface or coating, making it ideal for sensitive materials.
The Valgro Edge Breaker Series is the ultimate solution for achieving a uniform brush roughening effect that enhances powder coating and ensures a flawless finish. With its high productivity design, it eliminates the need for manual deburring, saving time and effort while delivering precise results every time.
- Precise Edge Deburring: The machine effectively targets burrs on the edges of fine blanking parts without impacting the surface. This ensures no deformation or surface damage, even on delicate components.
- Non-Aggressive to Coated Surfaces: It can be used on plastic-coated sheets without damaging or peeling off the coating, maintaining the protective plastic layer intact.
- Roller and Disc Brush Technology: The use of high-performance Roller and disc brushes ensures uniform burr removal while avoiding damage to part surfaces, making it ideal for sensitive and delicate materials.
- Adjustable Brush Pressure: The machine offers adjustable brush pressure to suit different material types and burr conditions, providing flexibility in operation.
- Dual Functionality: Suitable for both metal deburring and plastic-coated sheet deburring, making it versatile for mixed-material processes.
- Automated Process: The system is fully automated, ensuring consistent results with minimal manual intervention and reducing operator fatigue.
Benefits of Valgro Edge Breaker:
- Surface Integrity: The machine preserves the integrity of fine blanking parts and plastic-coated sheets by focusing only on the burr edges, making it ideal for precision applications.
- Enhanced Productivity: Automated edge deburring reduces manual labor, increases throughput, and provides consistent results, ensuring high efficiency in production lines.
- Cost Efficiency: Minimizing the risk of surface damage and reducing rework requirements leads to lower operational costs.
- Safe for Plastic Coatings: The technology ensures the safe deburring of plastic-coated materials, maintaining the functionality and aesthetic quality of coated products.
- Versatility Across Materials: The machine can work on various materials, including fine blanking parts and plastic-coated sheets, offering a broad range of applications in industries like automotive, electronics, and sheet metal processing.
A Brush Deburring Machine has a wide range of applications across various industries for precise edge finishing and surface preparation. Key applications include:
- Fine Blanking Parts: Used to remove burrs from fine blanking parts without damaging the edges or surfaces.
- Plastic-Coated Sheets: Ideal for deburring without harming the plastic protective layer, ensuring surface integrity.
- Laser-Cut and Punched Metal Parts: Effectively removes sharp burrs from laser-cut or punched metal components, improving safety and quality.
- Automotive Components: Enhances the finish of automotive parts by deburring edges for improved fitting and powder coating.
- Sheet Metal Fabrication: Ensures a smooth finish for sheet metal, reducing sharp edges for safety and further processing.
- Electronics: Deburrs and smoothens precision components used in electronic assemblies.
- Aerospace and Defense: Ensures precise deburring and finishing of critical aerospace components.
- Machinery and Equipment Parts: Improves the finish of various machine components, ensuring better assembly and longevity.
These machines are ideal for any industry requiring consistent deburring and surface preparation with high precision and safety.

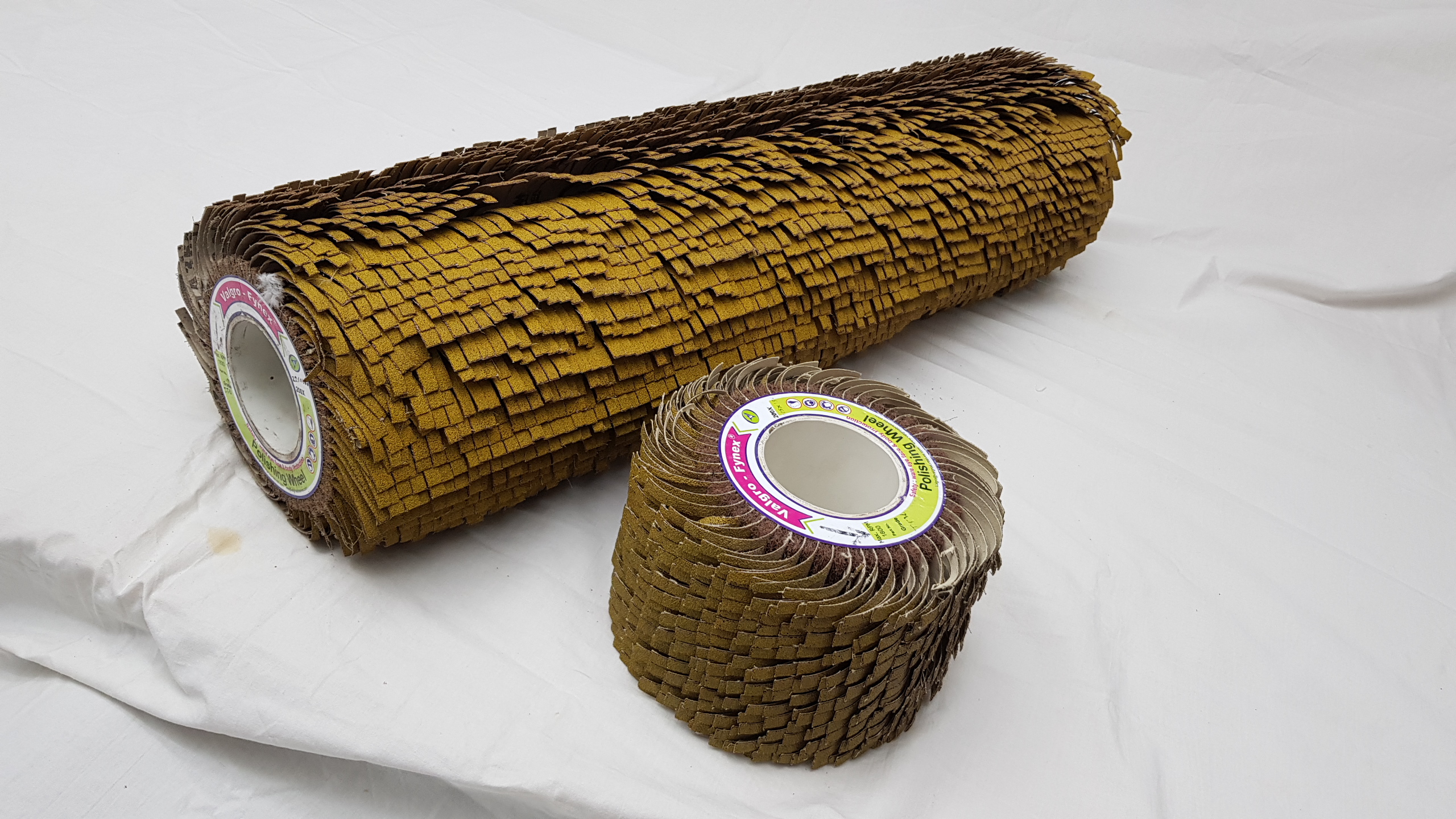
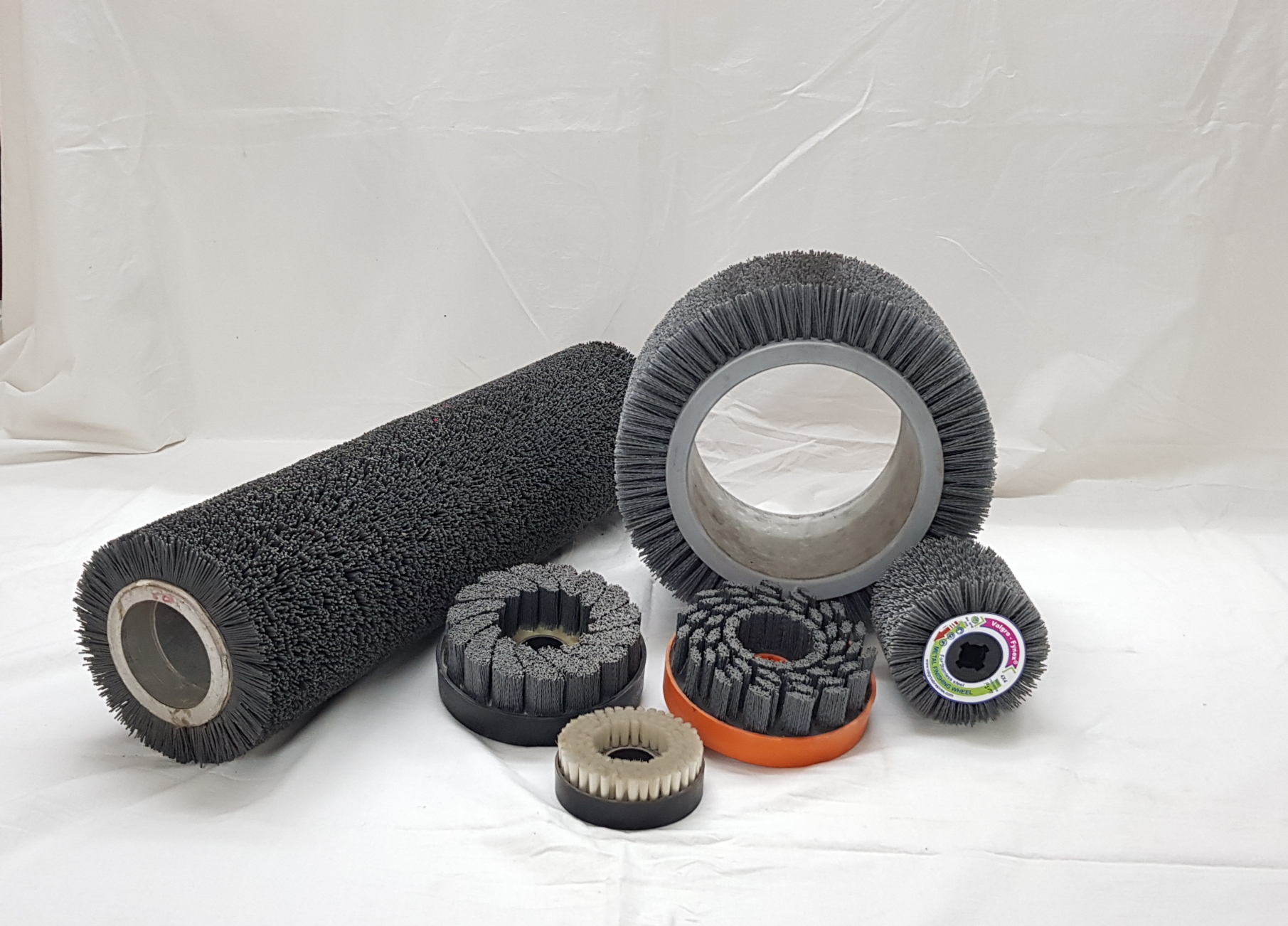
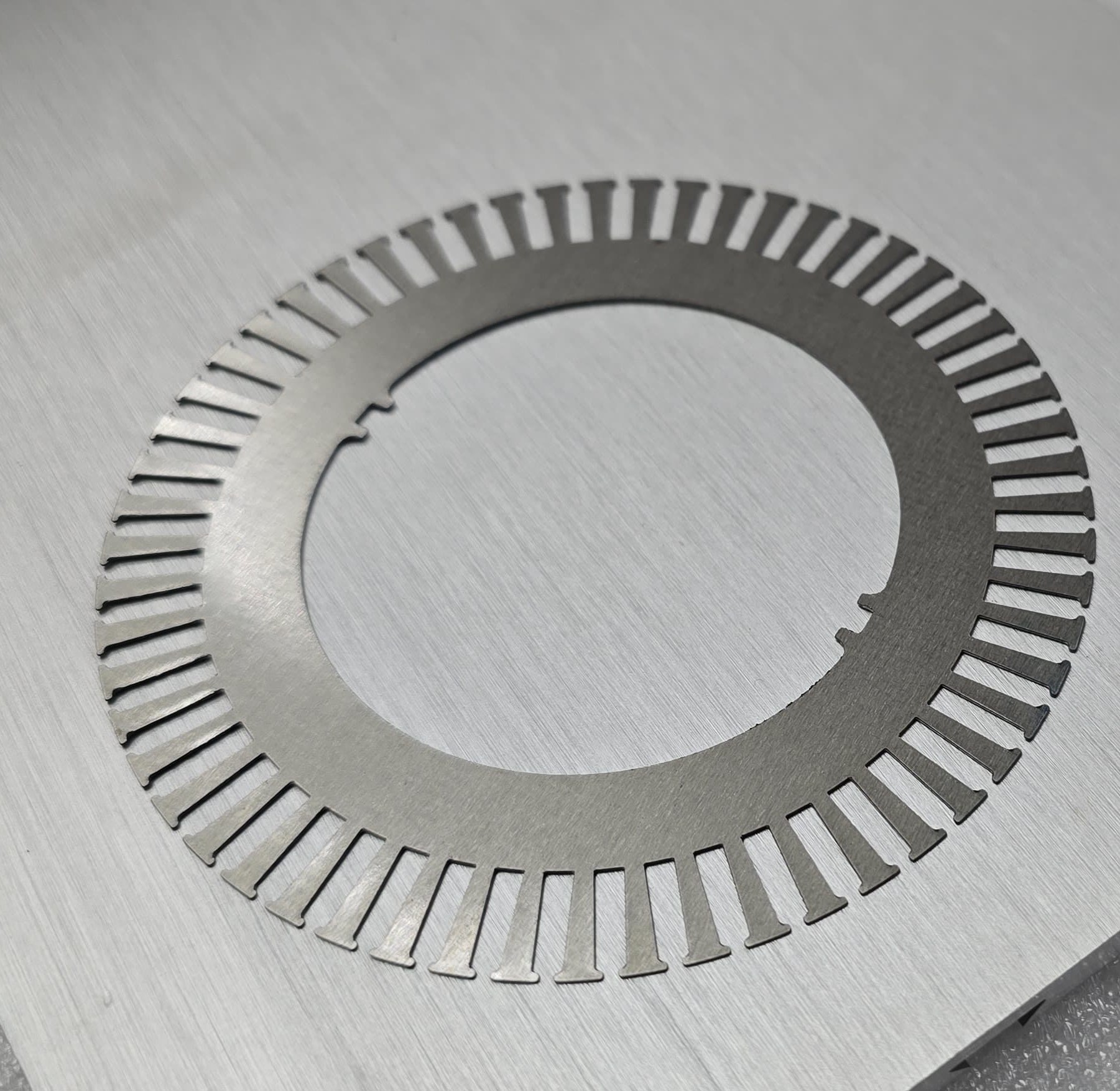
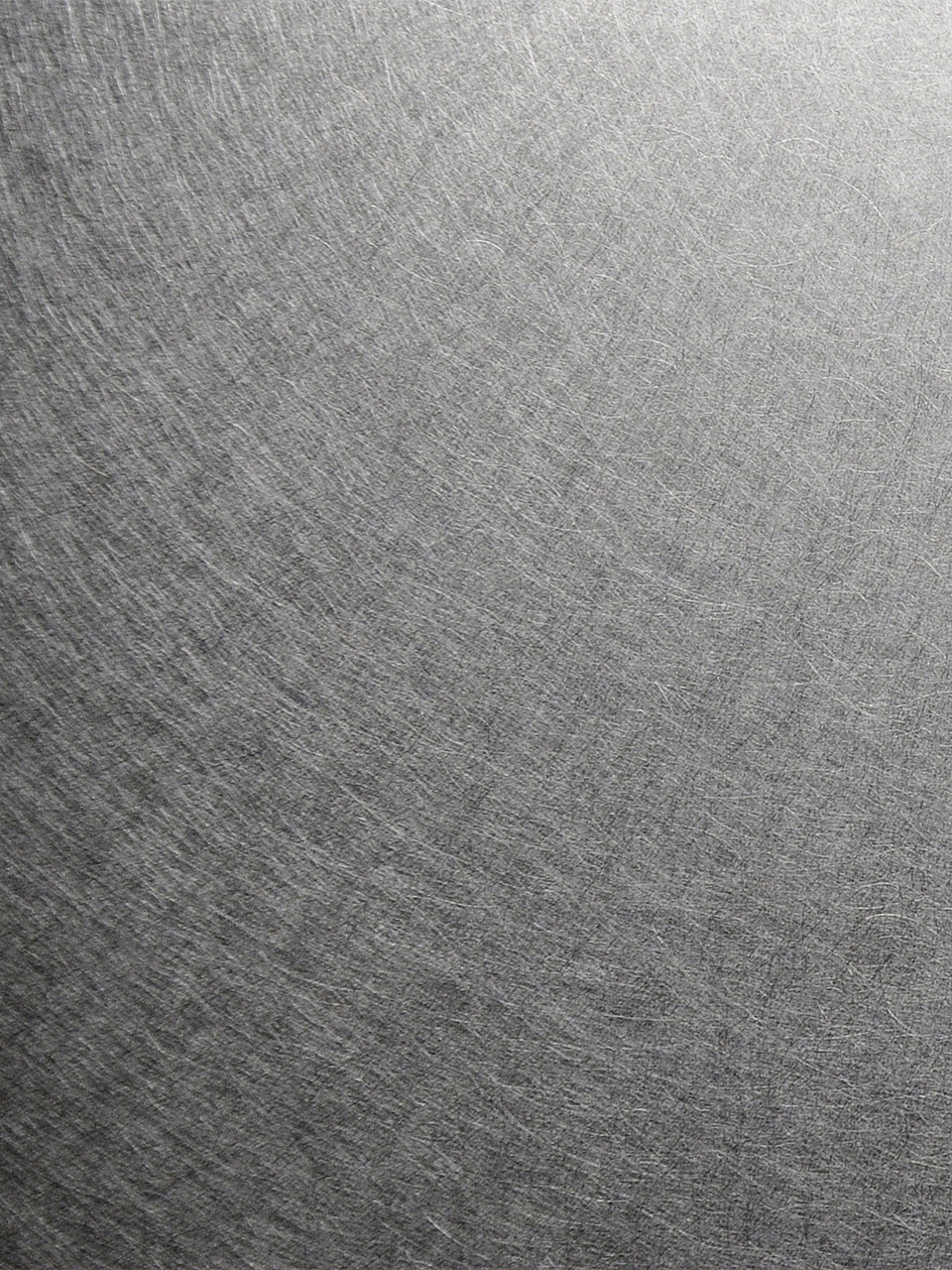
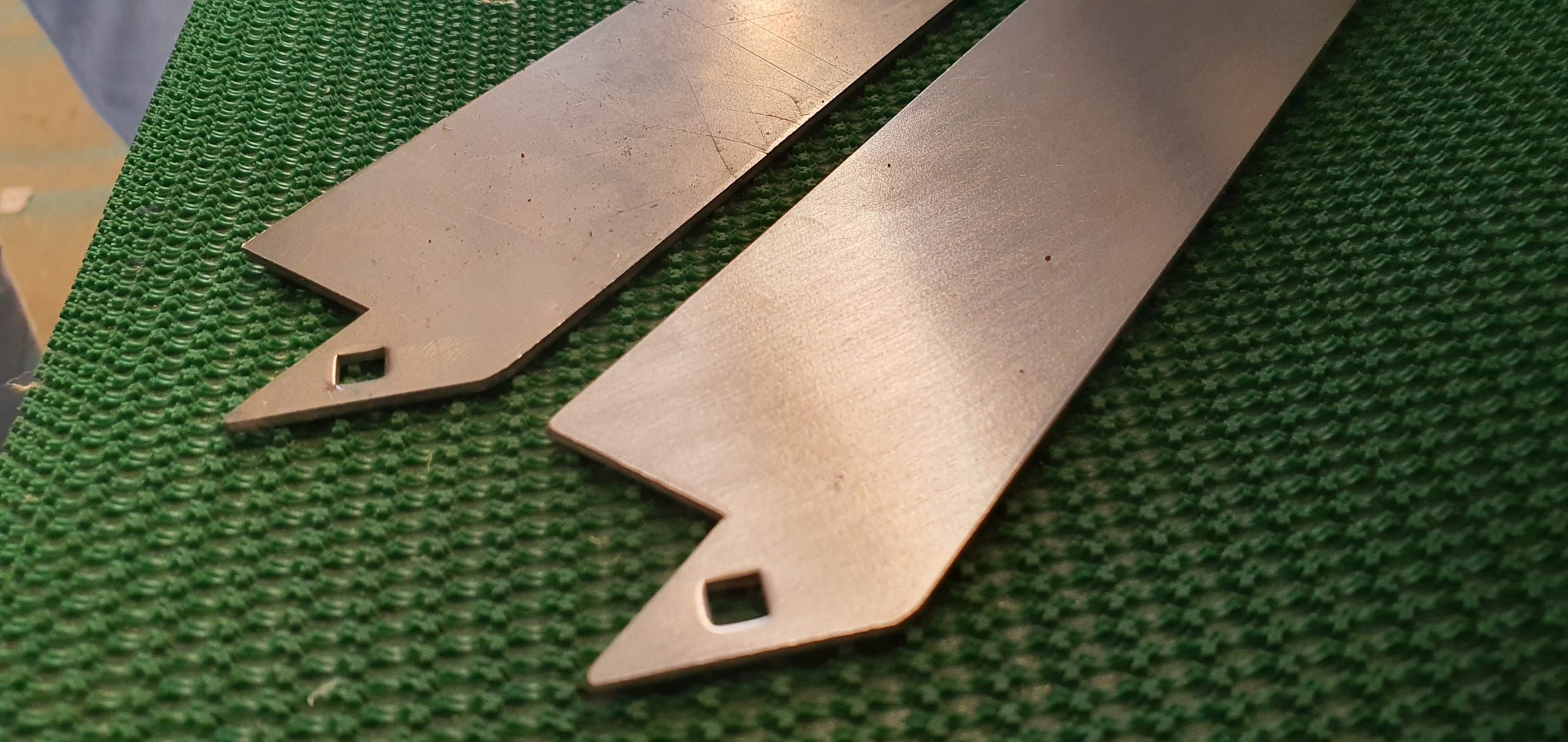
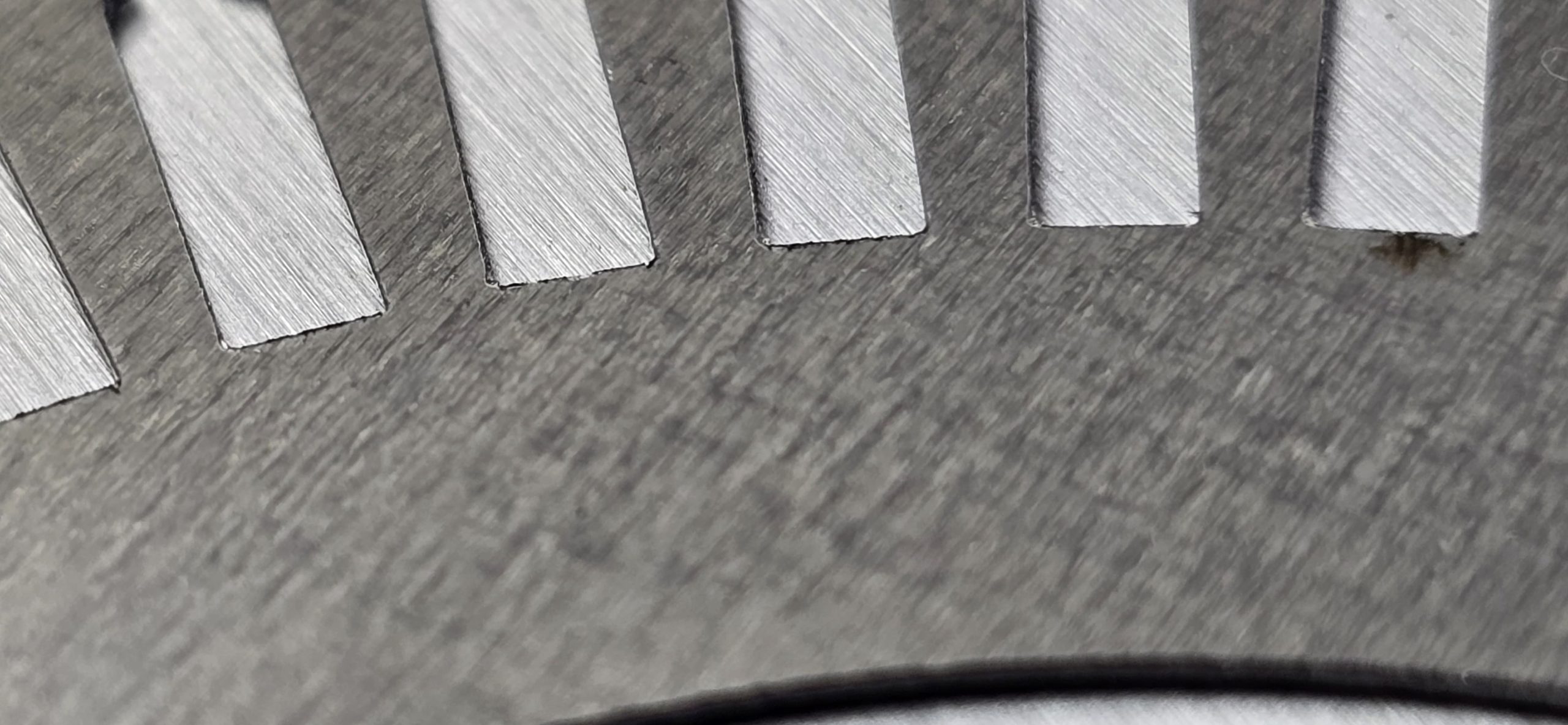