Electrical stamping involves the cutting and forming of thin sheets of metal, often used in motor laminations, transformers, and various electronic components. After stamping, burrs—small, raised edges or particles left on the metal surface—can pose several critical issues:
- High Precision: Delivers superior precision for the removal of burrs on extremely thin silicon stamped parts.
- Consistency: Guarantees uniform finishes across all parts, ensuring consistent quality in mass production.
- Increased Productivity: Reduces manual labor and speeds up the deburring process, improving overall efficiency.
- Cost-Efficiency: Minimizes the need for rework due to its precise deburring capabilities, saving time and material costs.
- Material Integrity: Preserves the structural integrity of thin silicon parts, preventing warping or damage during processing.
- Precision Deburring: Specifically engineered to handle thin silicon stamped parts (0.2 to 0.5 mm), ensuring no damage or distortion during the deburring process.
- Advanced Abrasive Technology: Equipped with cutting-edge abrasive systems for high accuracy, enabling fine deburring even in tight tolerances.
- Adjustable Speed Control: Variable speed settings allow users to fine-tune the deburring process, ensuring optimal results for different material types and thicknesses.
- Compact and Ergonomic Design: The machine’s space-efficient design makes it suitable for diverse industrial setups while maintaining user-friendly operation.
- Low Heat Generation: The machine operates with minimal heat, protecting sensitive silicon parts from potential thermal damage.
The Importance of Burr-Free Stamping:
Burr-free stamping is critical for ensuring the performance, reliability, and longevity of electrical components. Burrs, the unwanted imperfections left after the stamping process, can create a range of problems that affect both the electrical and mechanical properties of the parts. Ensuring that stamped parts are free from burrs is essential for maintaining the high standards required in industries such as electronics, automotive, and power generation. Two fundamental aspects of this are electrical efficiency and dimensional accuracy.
Electrical Efficiency: Burrs on electrical components can disrupt the flow of electricity, creating resistance that leads to inefficiencies, energy loss, and potential heat buildup. This interference can negatively impact the overall performance of the device, decreasing its efficiency and potentially shortening its lifespan. By ensuring a burr-free surface, electrical components can maintain optimal conductivity, minimizing energy waste and enhancing the reliability of the system.
Dimensional Accuracy: Burrs can distort the precise dimensions of stamped parts, affecting their fit and function within an assembly. Even small deviations caused by burrs can lead to improper alignment, operational issues, or even equipment failure. A burr-free stamping process preserves the dimensional integrity of components, ensuring they fit perfectly in assemblies and function as intended, without compromising performance or safety.
In electrical stamping, burr-free surfaces are essential to ensure optimal performance and reliability of components used in industries such as electronics, automotive, and power generation. Burrs, which are tiny raised edges or imperfections left after stamping, can interfere with electrical conductivity, affect mechanical assembly, and lead to premature failure of parts.
Valgro’s Electrical Stamping Deburring Machine is specially designed to address these challenges. It is ideal for applications such as motor laminations, transformer cores, and other electrical components that require precision deburring for efficient performance. Our advanced deburring technology ensures smooth surfaces, improving electrical flow, minimizing energy loss, and reducing wear and tear in high-precision assemblies.
By offering consistent, high-quality results for stamped parts as thin as 0.2 to 0.5 mm, Valgro’s machines help manufacturers achieve the level of precision required for critical electrical components, enhancing their efficiency, durability, and overall quality.
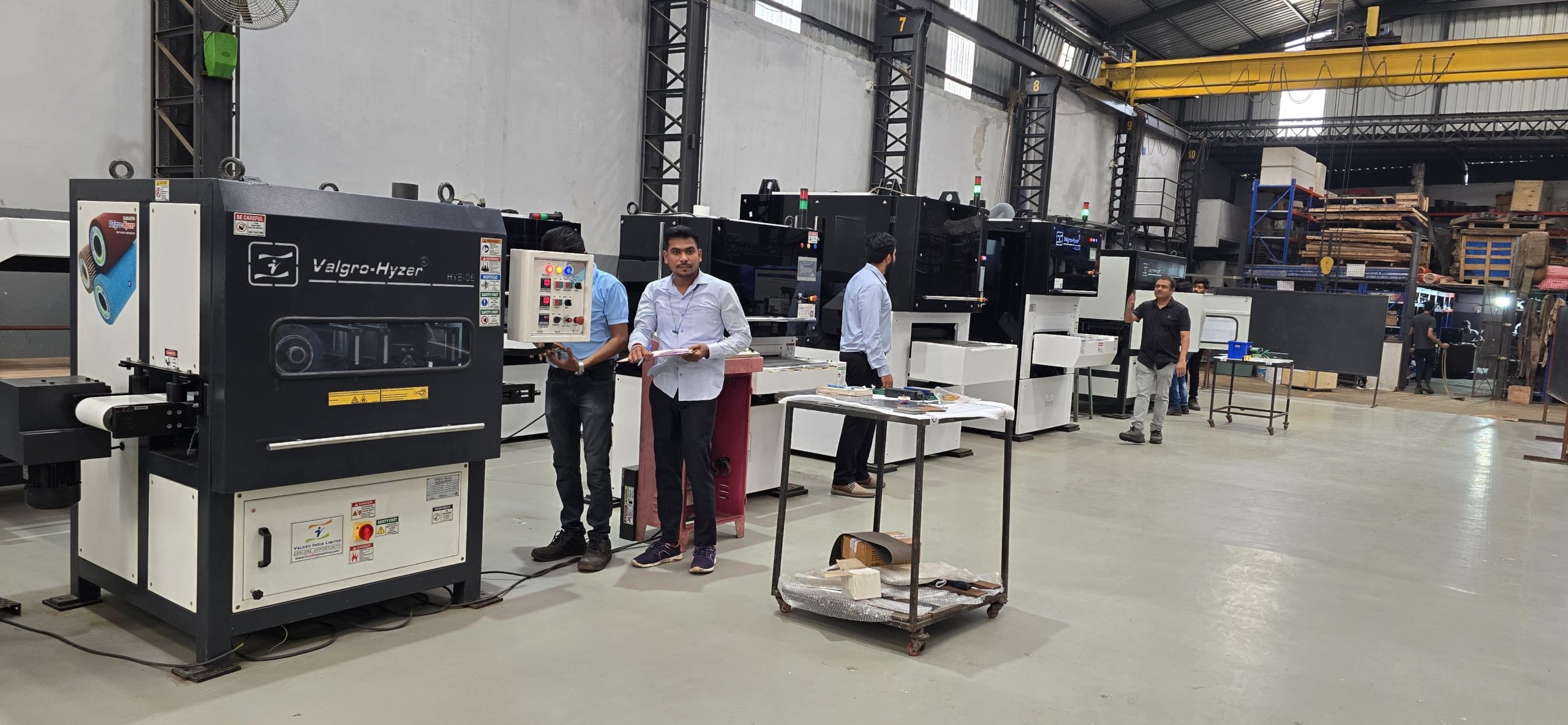
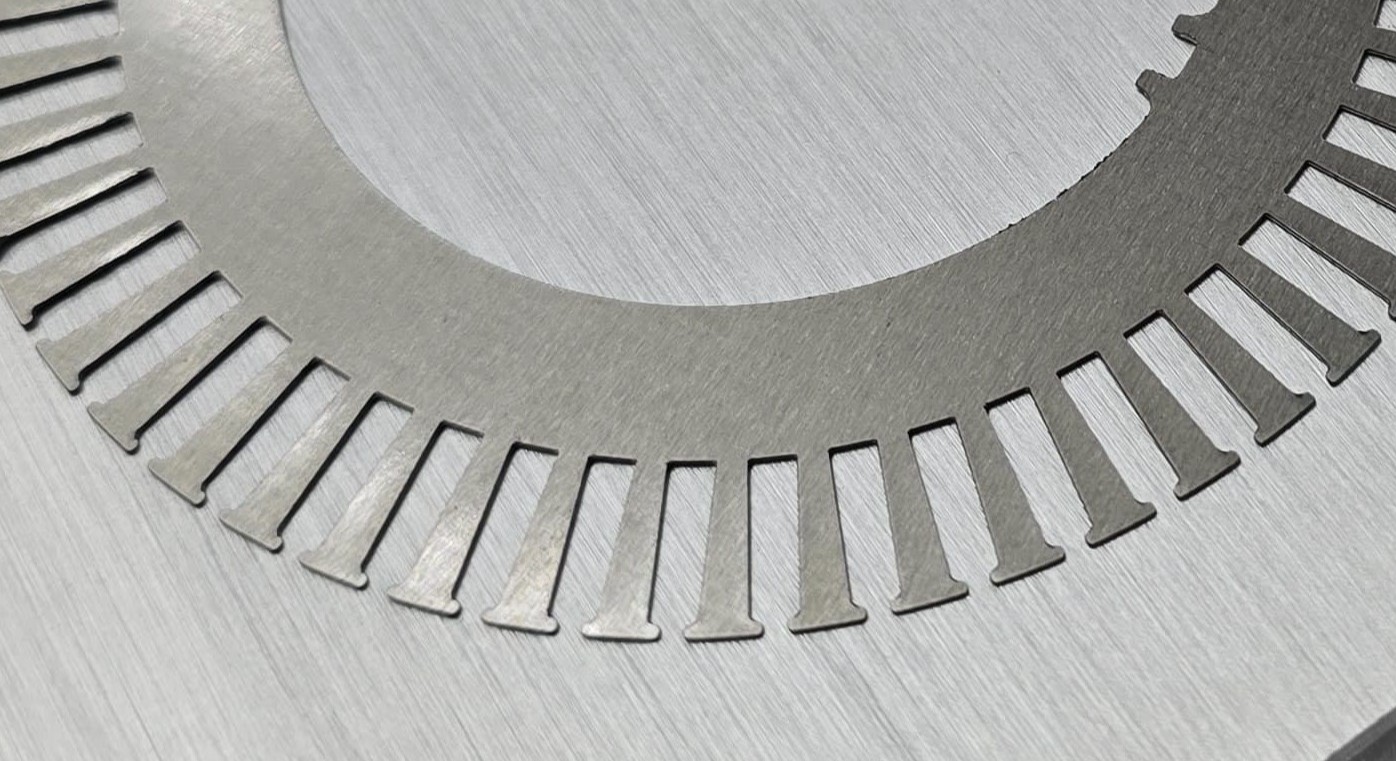
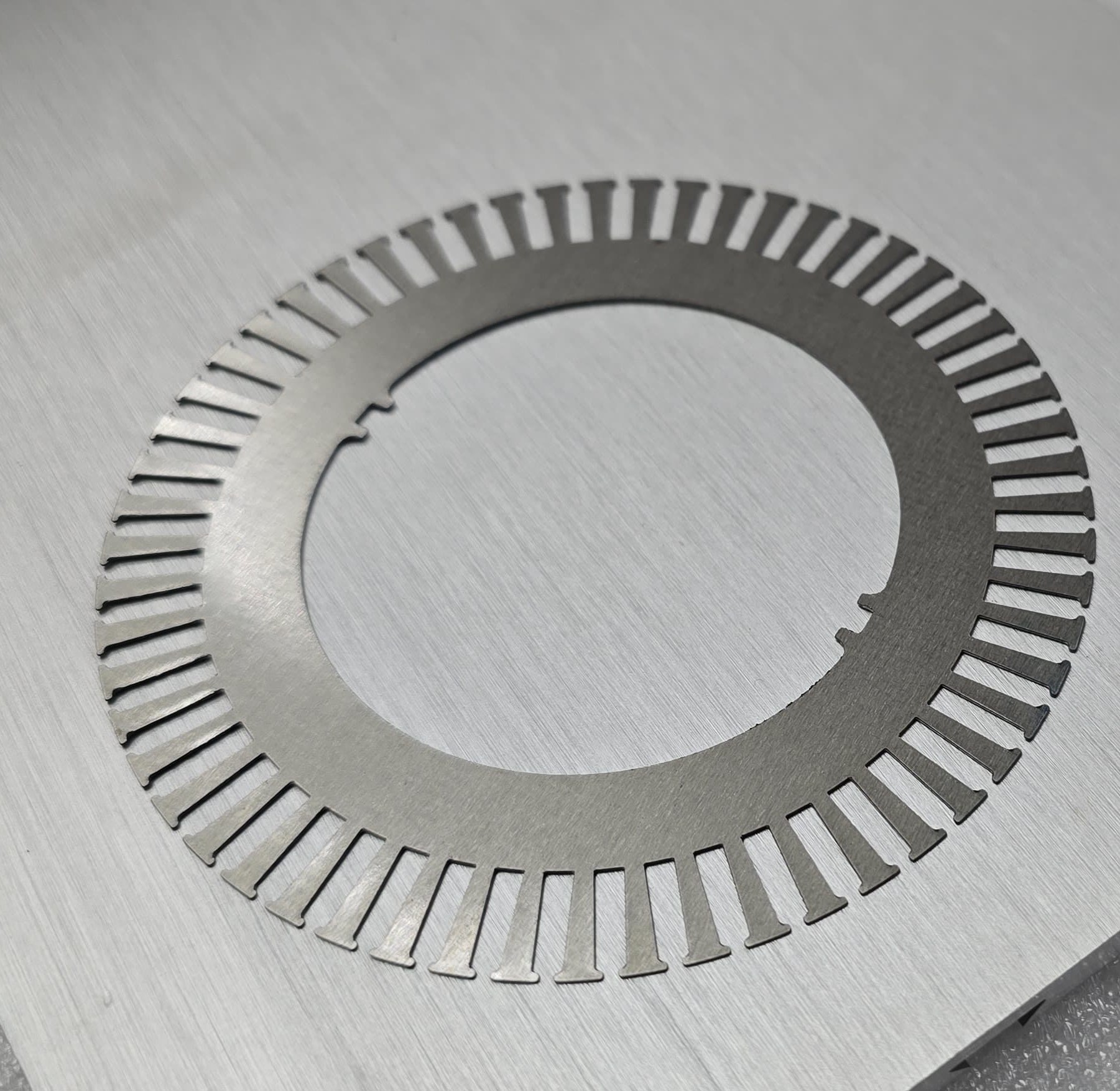
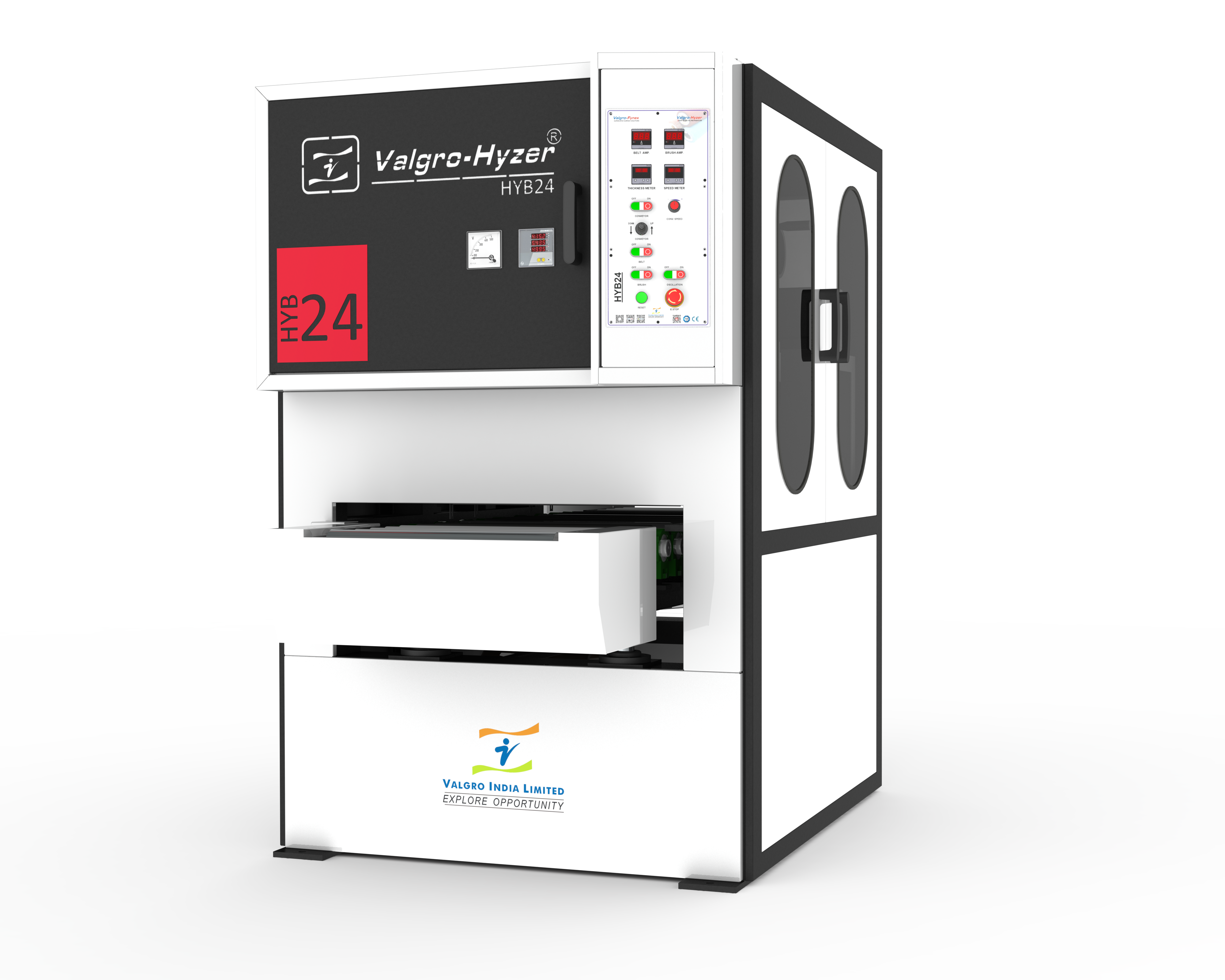